The Food Recycle Process
We collect one of the world's most problematic wastes and turn it into one of the world's most sought after resources.
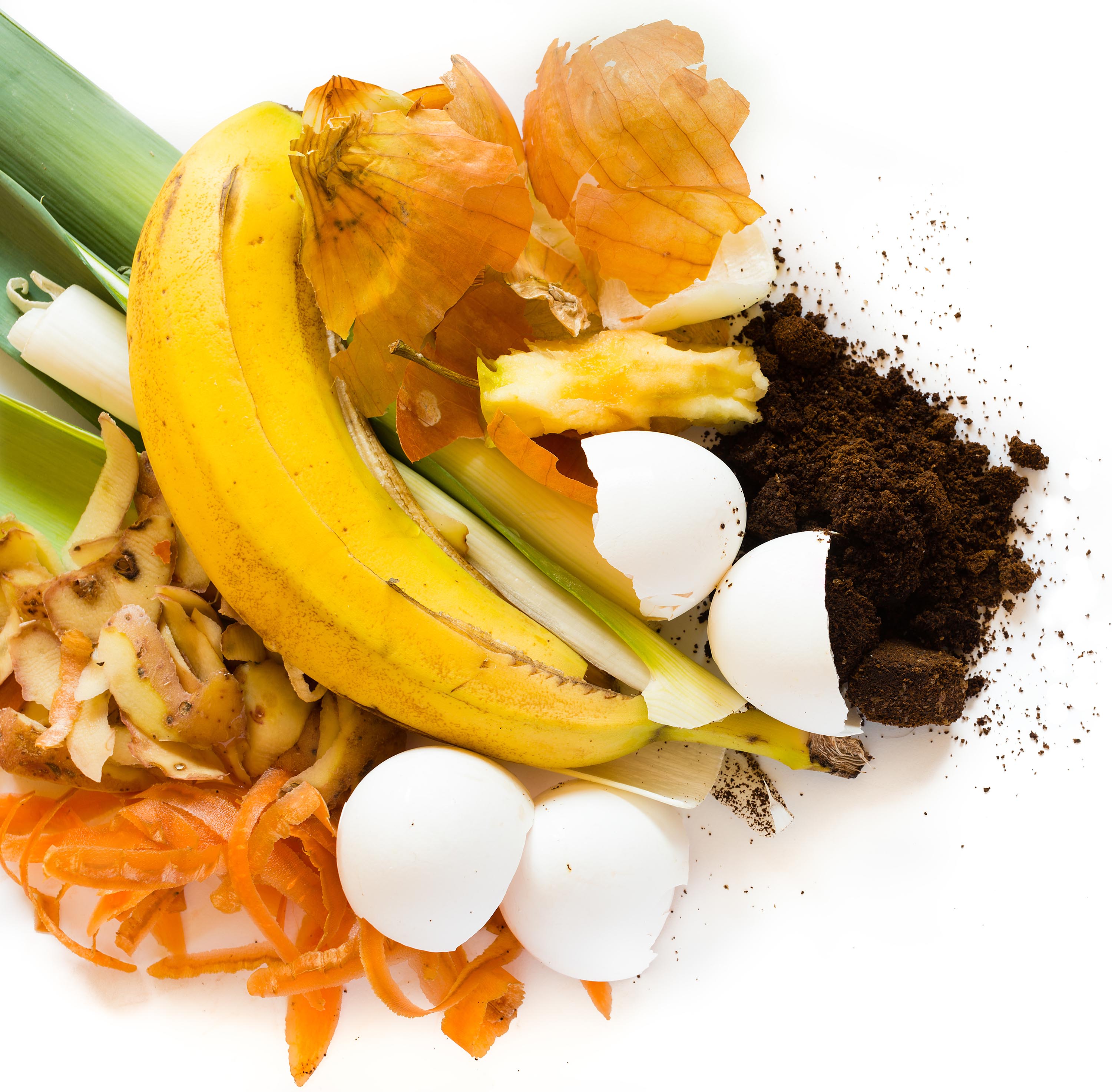
How we do it
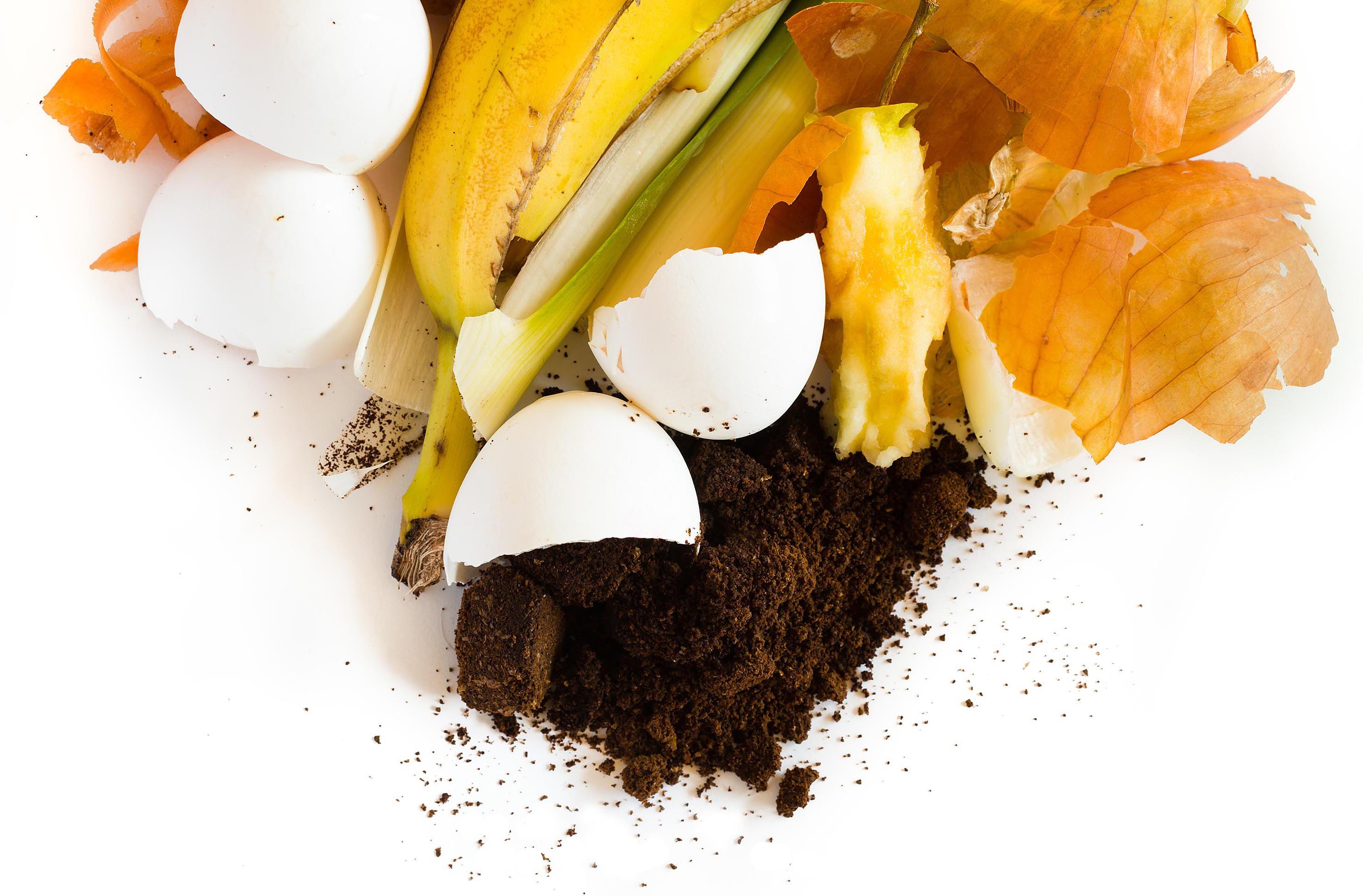
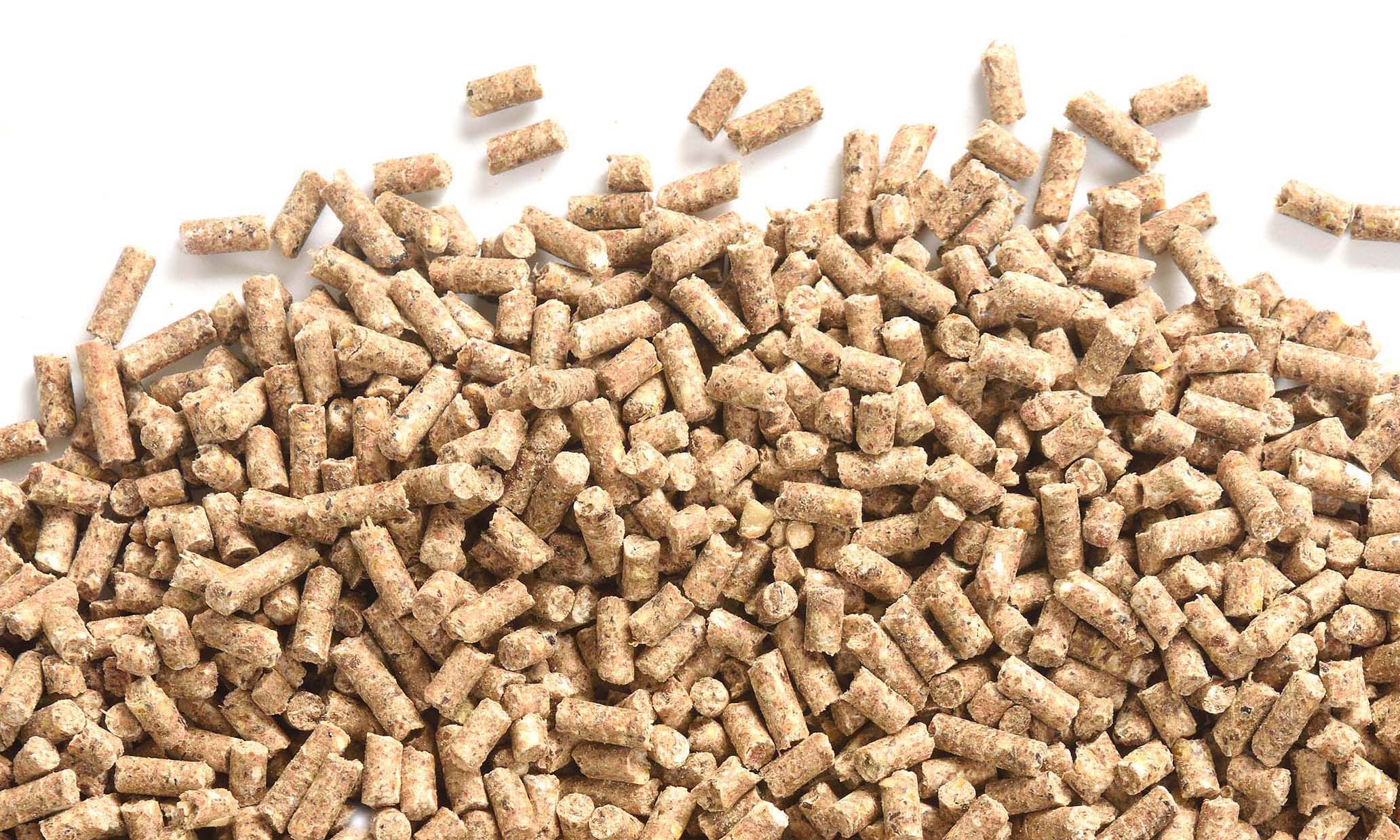
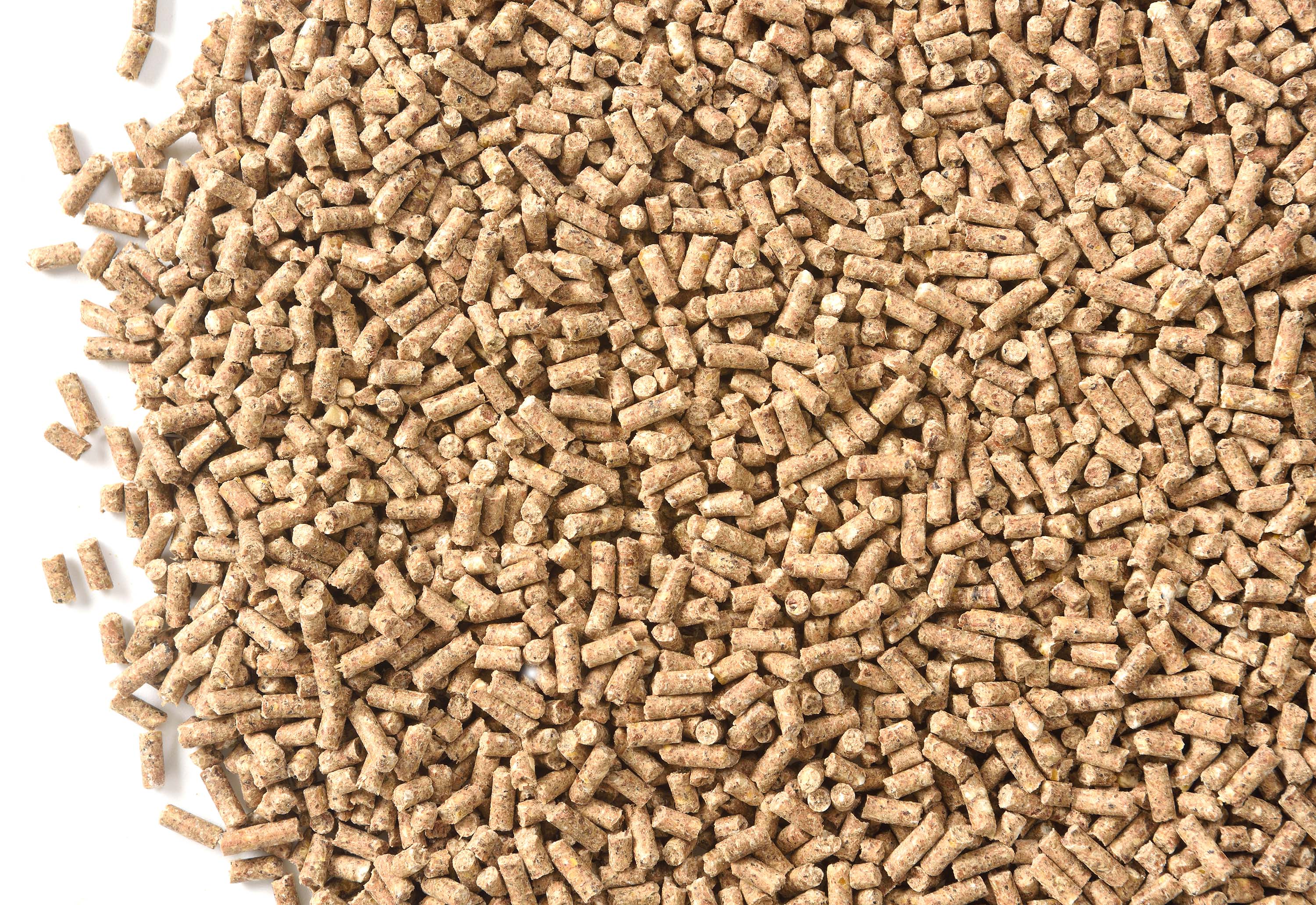
The technology
Our technology consists of five key steps to convert food waste into animal feed.
A fundamental point of difference of the Food Recycle technology is that we collect and process different waste streams separately. This enables us to store different dry materials of similar nutritional value and use them as ingredients when formulating our complete feeds.
Each waste producer is profiled into a category based on the average nutritional profile of their waste. The food waste is collected from the waste producer and kept separate with other waste of the same profile.
Each waste stream is processed separately through the facility. This includes a biosecurity step that kills every known pathogen associated with food waste.
Once processed, each waste stream is stored in silos as a dry granulated powder. Each silo's content is then tested for it's nutritional content and amino acid profile.
Multiple ingredients from different silos are then mixed together with any required micro-ingredients for each formulation.
The completed feeds are then pelletized (if required) and packaged according to their end use.
What is the food to feed ratio?
The Food Recycle process produces roughly a 50% output of animal feed from food waste, with the single by-product of evaporated water.
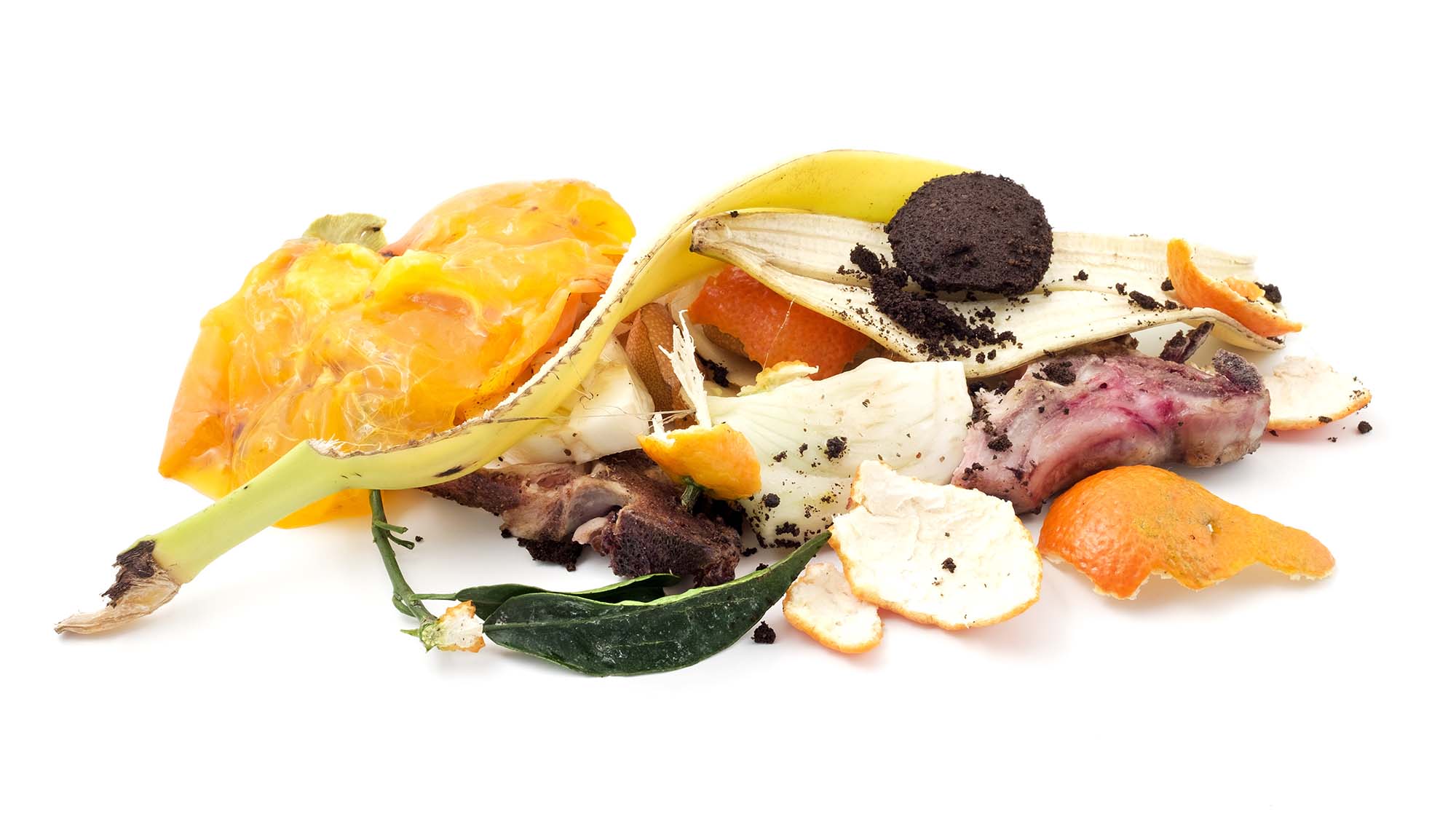
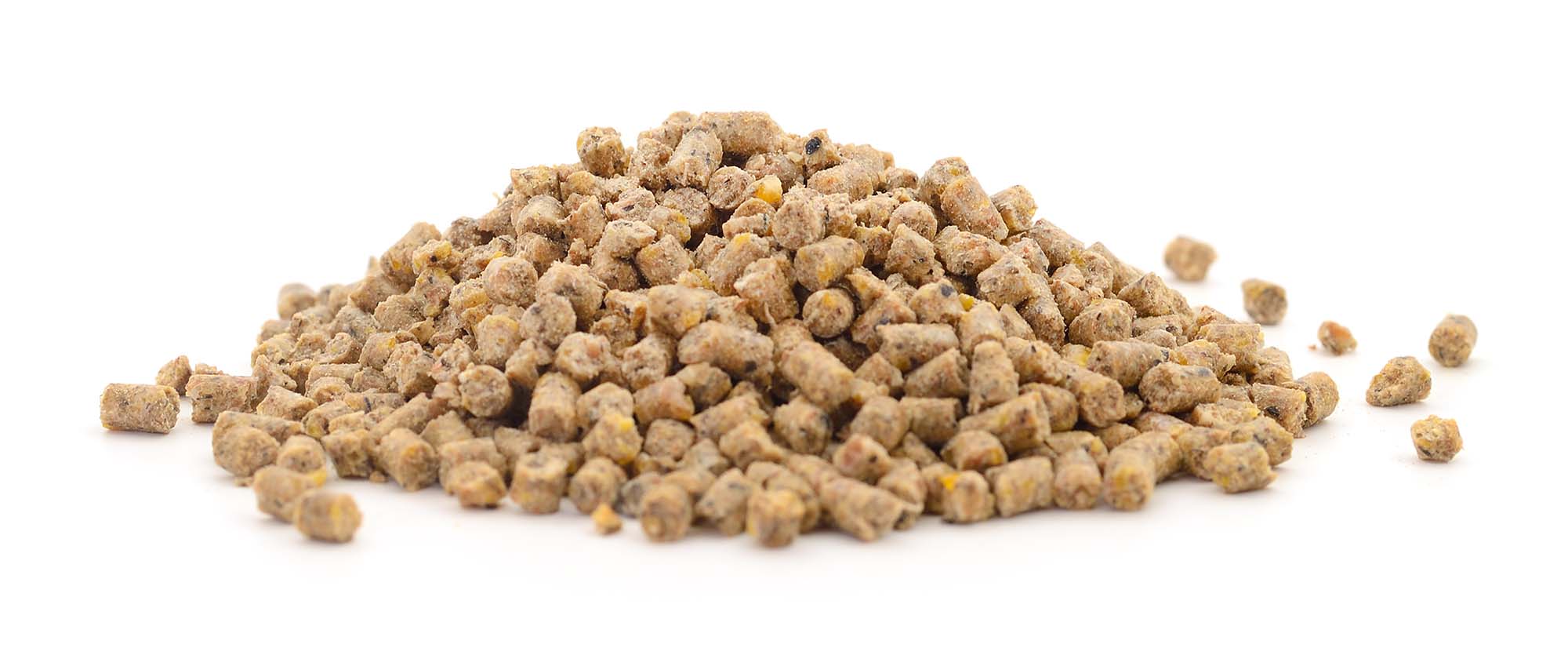
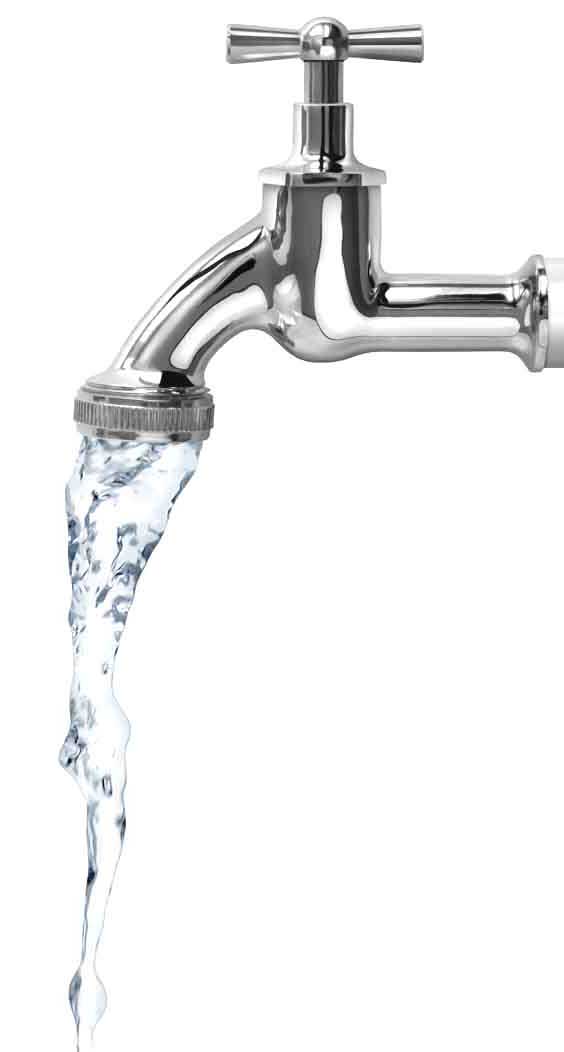
What type of animal feeds does the process produce?
The Food Recycle process produces high performance complete feeds for the pig, poultry and aquaculture industries. Every country in the world has at least one of these industries on their doorstep.
Explore our Resource Centre for some of our documented feed trials
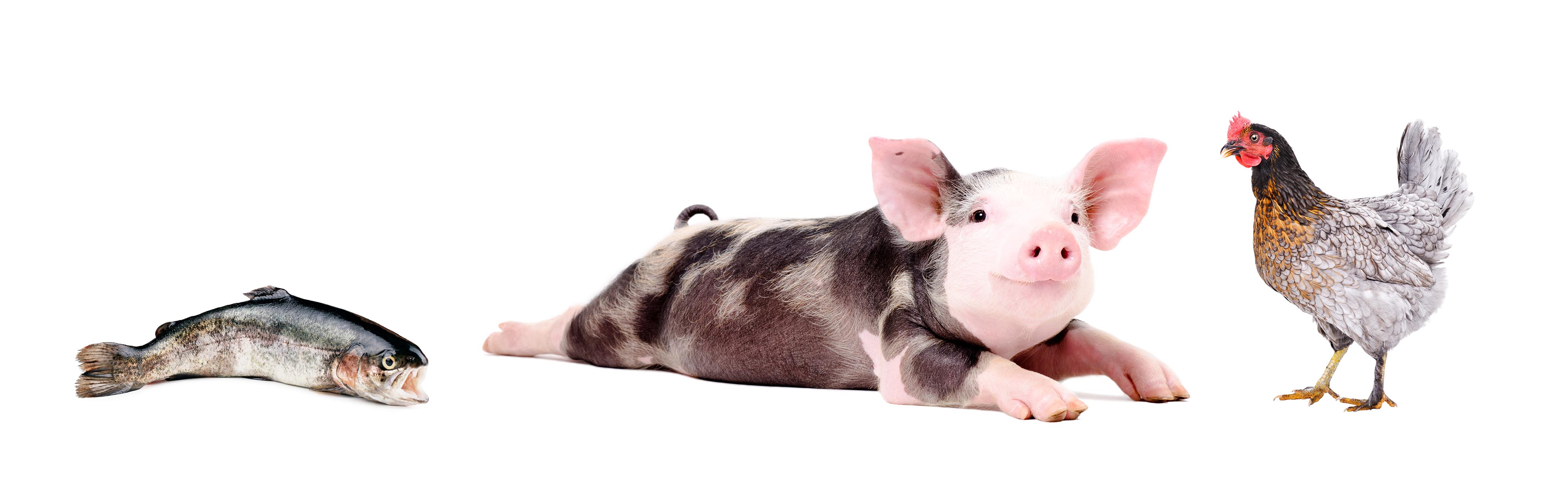
Unlike other processes that make a single ingredient to add to supplement feeds, our process produces complete feeds made up of up to 99.1% food waste. This ensures that we are using all the food waste available, not just the sources high in protein and it also displaces more raw ingredients that are used in making feeds.
Yes. Different levels of contamination are collected at different costs. The less contamination, the less cost to the waste producer for collection.
Yes, our technology includes a "kill step" that inactivates all known biosecurity threats present in food waste.
A big yes. Even if we converted all of the food waste in the world into feeds, we would not have enough feeds to service the markets of pig, poultry and aquaculture.
Not currently, at this point in time our feeds are only suitable for pig, poultry and aquaculture due to the presence of meat products in the food waste sources.
Contact us
Fill out the form below and we’ll get right back to you
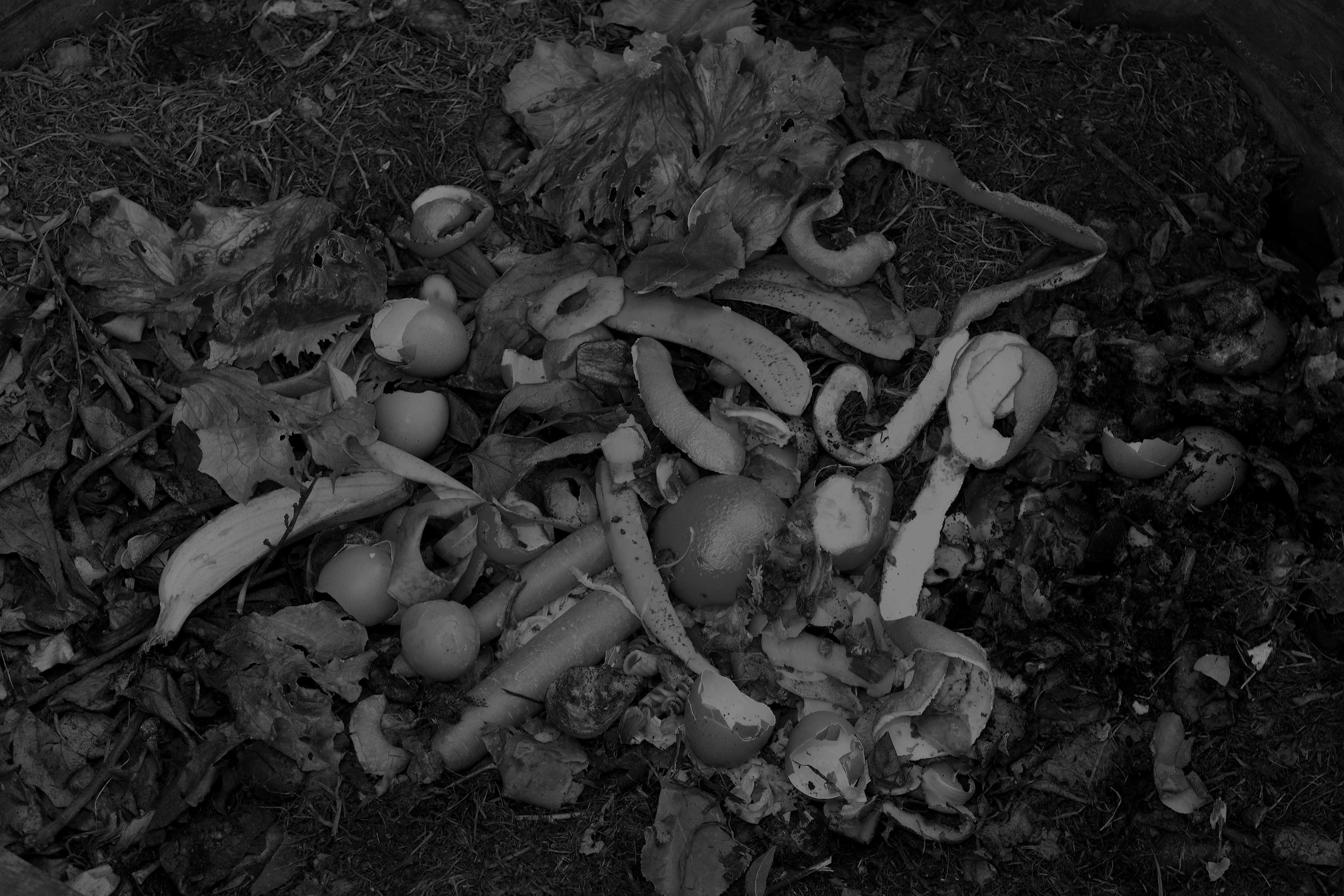